The world of construction is both essential and ever-evolving. As we continue to build homes, offices, and various structures, the search for sustainable construction materials becomes increasingly crucial. This quest not only focuses on eco-friendly materials, but also on the sustainability of the processes involved in creating them.
Amidst the abundant waste in our world lies untapped potential, waiting to be transformed into something more useful than mere biomass. Enter CornWall, a new player in the realm of interior wall cladding, born from an unexpected source: corn cobs.
What Is Cladding?
Cladding in the construction world is like putting a protective and stylish coat on a building. It dresses a structure in layers for aesthetics and protection from the weather. Cladding acts as a barrier, keeping the building safe and sound. Plus, it can be made from all sorts of materials – metal, wood, stone, and even recycled stuff like corn cobs, giving buildings their unique outfits while keeping them protected.
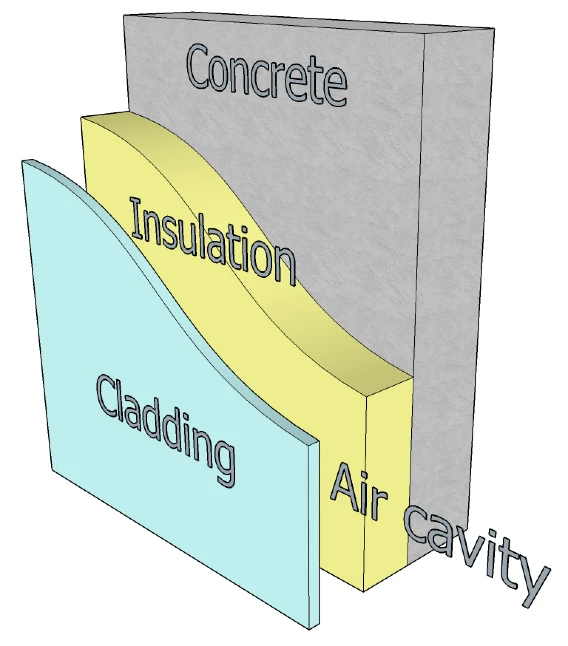
Created by StoneCycling and Studio Nina van Bart, CornWall represents a fresh approach to interior wall cladding. This product leverages organic corn cobs, exposing them to temperatures up to 150 degrees Celsius (302 degrees Fahrenheit). This heat activation process forges strong bonds, making the material sturdy and durable.Â
But CornWall’s commitment to sustainability doesn’t stop with its base material. The heating process itself is environmentally conscious, utilizing sustainable energy sources. The factory’s solar panels power the electric heaters, ensuring the manufacturing process leaves minimal or no carbon footprint.
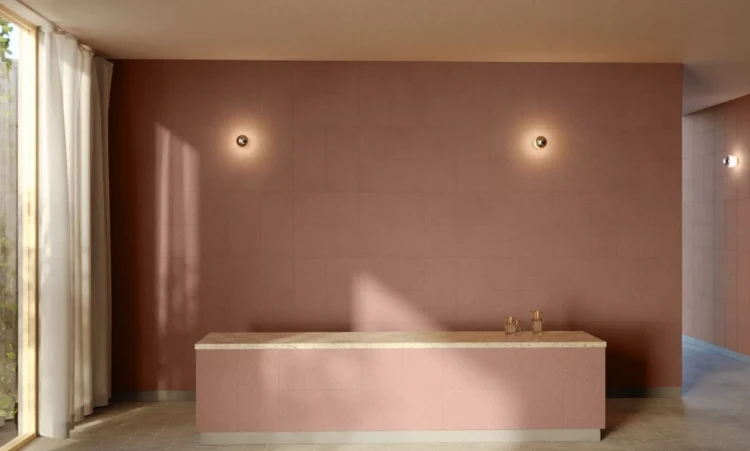
Traditionally, corn cobs have been underutilized, often left in fields, fermented, or burned as biomass. CornWall, however, transforms these cobs into a valuable construction material, offering an innovative alternative to conventional ceramic wall cladding or composite materials like high-pressure laminate (HPL).Â
One significant benefit of CornWall is its ability to store more carbon dioxide, thanks to the CO2 already absorbed in the corn cobs.
Additionally, it boasts a 100% reusability factor. Its demountable anchoring system allows for easy removal and reapplication, enhancing its eco-friendly credentials.
Visually, CornWall aligns with the aesthetics of traditional wall cladding, resembling the familiar look of cork coasters. It’s available in a variety of colors, including Dark Blue, Mustard Yellow, Terracotta Pink, etc., blending functionality with style.Â
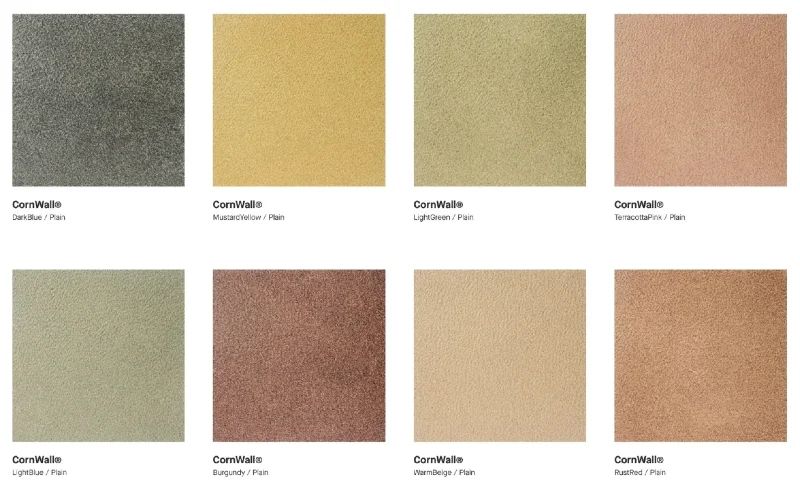
The hope is that CornWall paves the way for more construction materials that prioritize sustainable materials and processes, steering the industry towards a more environmentally responsible future.
CornWall's Sustainability
CornWall’s innovative approach lies in its unique use of corn cob waste, a material that would otherwise contribute to biomass waste. By recycling this agricultural byproduct into a building material, CornWall reduces the environmental impact typically associated with construction materials.
The process of transforming corn cobs into CornWall covering is itself a model of sustainability. The corn cobs are subjected to a high-temperature treatment, but this process is powered by renewable energy from solar panels, exemplifying a closed-loop, low-impact manufacturing cycle. This method significantly reduces the carbon footprint compared to traditional material production, which often relies on fossil fuels.
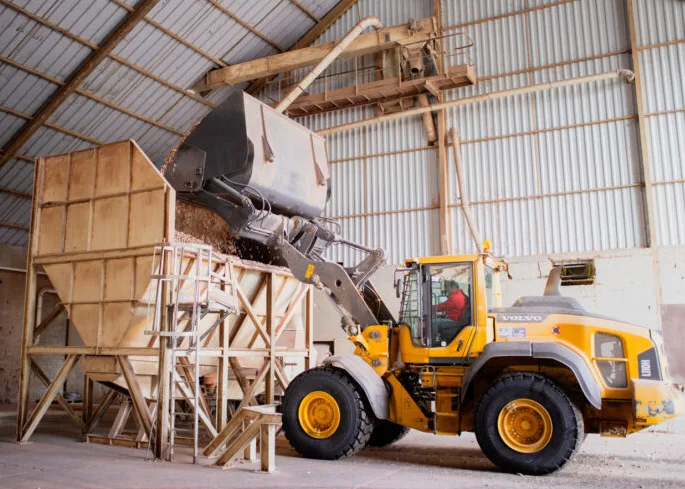
CornWall covering also addresses the critical issue of carbon sequestration. The corn cobs, having absorbed CO2 during their growth, retain this carbon dioxide, preventing its release into the atmosphere. This characteristic makes CornWall a carbon-negative material, a rare and valuable trait in building materials.
Moreover, CornWall’s 100% reusability is a significant advantage over many construction materials. Its demountable anchoring system allows for easy removal and reinstallation, promoting a circular economy approach where materials are reused rather than discarded.
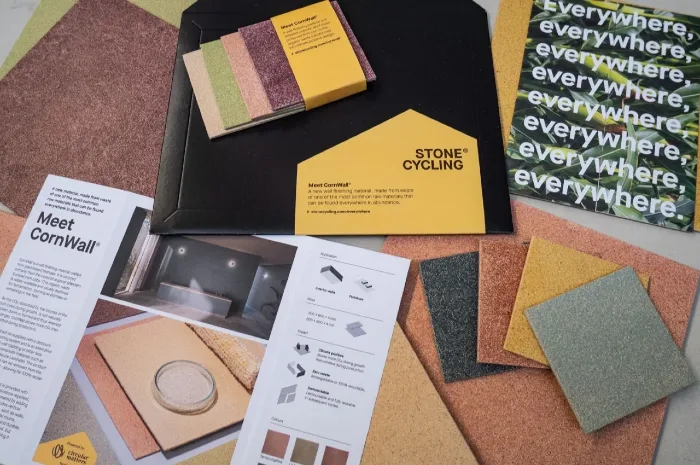
Balancing Pros and Cons
Despite its numerous advantages, CornWall is up against the same challenges most sustainable products face. Its manufacturing process, while eco-friendly, may involve higher costs due to the use of renewable energy and sustainable practices. This factor could make CornWall more expensive than traditional cladding materials, potentially limiting its accessibility.
Beyond the practicalities of mass production, the long-term durability and performance of CornWall compared to conventional materials like ceramic or HPL are unknown.
While its eco-friendly attributes are clear, its practicality and longevity in various environmental conditions need further assessment.
How It's Made
Cultivating
Maize is the most common and popular crop grown globally. The maize market is estimated to be worth $143.62 billion currently, and is expected to reach $166.57 billion by 2029. Maize is a cereal grain, commonly known as corn. Much of the consumed corn is separated, leaving the cob to be discarded as waste or burned as biomass.
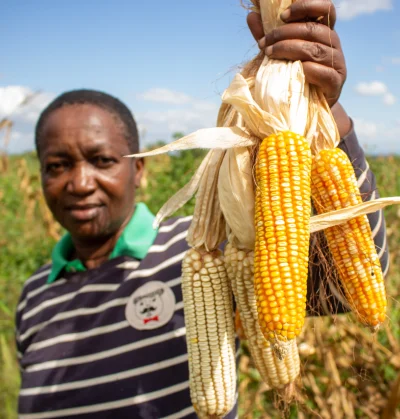
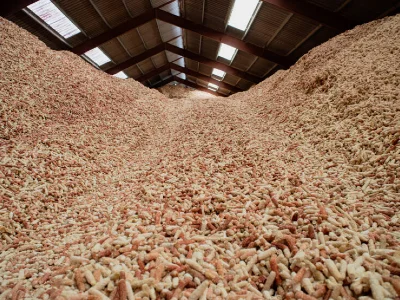
Collecting & Drying
These corncobs that would otherwise degrade on the field, be discarded, or burned as biomass (in all cases the carbon that’s locked in the cobs is released), is collected and dried indoors.
Shredding
Once dried, the cobs are shredded into a fine powder to be used as the main ingredient for CornWall.
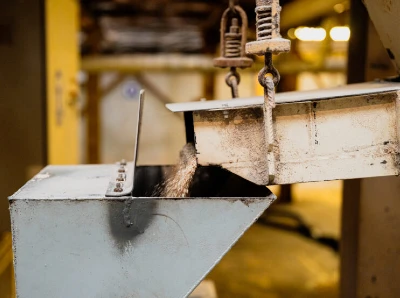
But How Much Of A Difference Could This Really Make?
The construction industry, while vital to our modern lives, is a major environmental concern. In fact, this sector is responsible for roughly 39% of global carbon emissions, with 28% coming from building operations and a staggering 11% from construction processes and materials production.
Let that sink in for a moment! Imagine the vast amounts of steel, concrete, and other materials produced each year – all contribute to this hefty carbon footprint. Sadly, the damage doesn’t end there. Construction activities release a plethora of pollutants into the air and water.
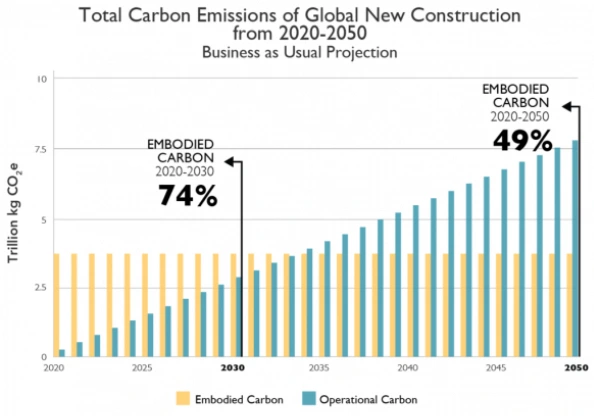
If the construction industry globally embraced such eco-friendly solutions like CornWall, the impact would be massive. Switching to materials like CornWall could drastically reduce the sector’s carbon emissions and with the material’s ability to store carbon dioxide already absorbed by corn cobs, we’re not just reducing emissions; we’re actively removing CO2 from the atmosphere. This shift would turn buildings from carbon sources into carbon sinks.
Because we know the entire process behind CornWall, we can confidently say that it uses considerably less energy throughout the manufacturing processes.Â
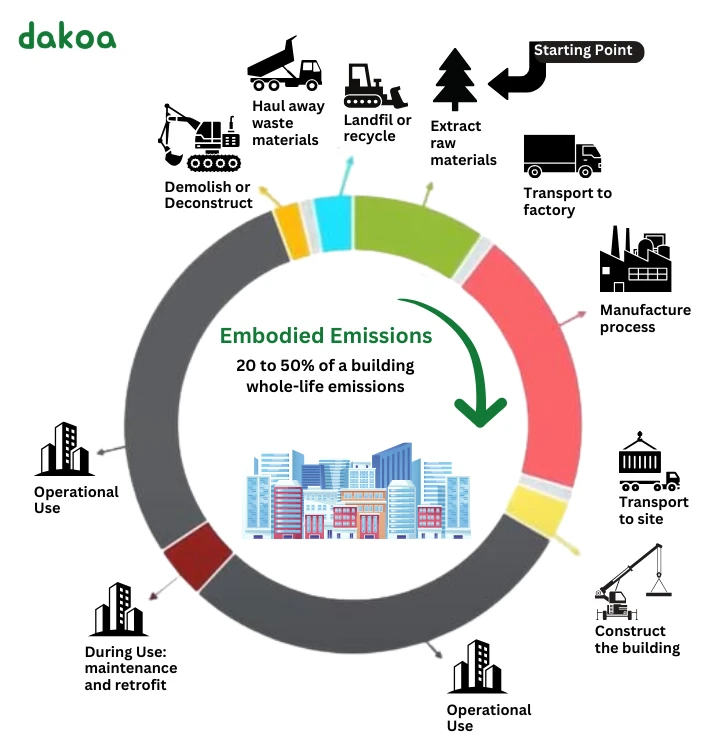
If widespread adoption occurred, the industry would see a significant drop in energy consumption. And then there’s the ripple effects: cleaner air, less strain on natural resources, and a major step towards combating climate change.
If this were to happen, buildings wouldn’t just provide shelter; they’d be active participants in healing our planet. It’s a change that goes beyond numbers; it’s about reimagining our world where every brick and panel contributes to a healthier, greener future.
In conclusion, CornWall represents a significant step towards sustainable construction, offering an innovative solution that repurposes agricultural waste into a valuable building material. Its eco-friendly manufacturing process and potential for carbon sequestration set it apart from traditional materials.Â
More To Discover
- Meet reU: The Cardboard Bottle Changing How We Drink Water Sustainably
- Bio-Composite Roof Tiles with Solar Panels: A Modern, Sustainable Nod to Traditional Craftsmanship
- Puzzle-Inspired Electric Minivan: Where Modular Design Meets Sustainability – Ugly Yet Promising
- Fin-Driven Motor: FinX Introduces Propeller-Free Boating
However, like all pioneering products, it faces challenges in cost and long-term performance. As the industry continues to evolve, it’s hoped that materials like CornWall will inspire further innovations in sustainable construction.
Meet The Designer: StoneCycling
As a student in 2012 at the Design Academy in Eindhoven, Tom van Soest developed a blender to crush waste materials such as sinks, tiles and glass. It became the basis for StoneCycling, a company that creates bricks from ceramic, glass and other insulation material.